Are you a Dipper also ?
Not being the most proficient TIG welder I sometimes dip the tungsten in the weld pool and contaminate it. This means a re-grind of the tip. I don’t have a dedicated grinding wheel so the grinding process has the potential to fundamentally contaminate the tungsten from the wheel while re-grinding. This got me thinking whether I could use my Dremel with a dedicated grinding wheel that would be reserved just for tungsten grinding.
I decided that my design would be based around my most used two tungsten diameter sizes (1/16” and 1/8”) and I would aim for 15°, 30° and 60° inclusive grinding angles.
I have always been nervous about tungsten dust and even more so knowing that some tungsten materials are radioactive so my design would enclose the grinding process and a viewing window would let me see what was going on.
The design is not ideal because the recommendation for grinding tungsten is to have the grinding striations running in line back down the cone of the point and not around the point. The final result depends on the speed of the Dremel and the speed of rotation of the tungsten being ground.
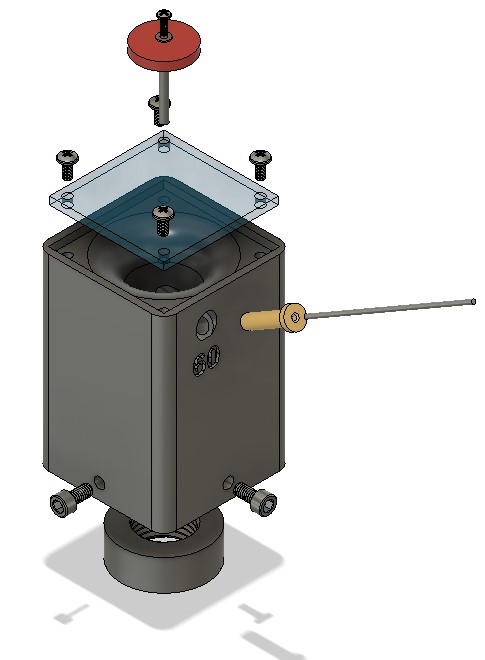
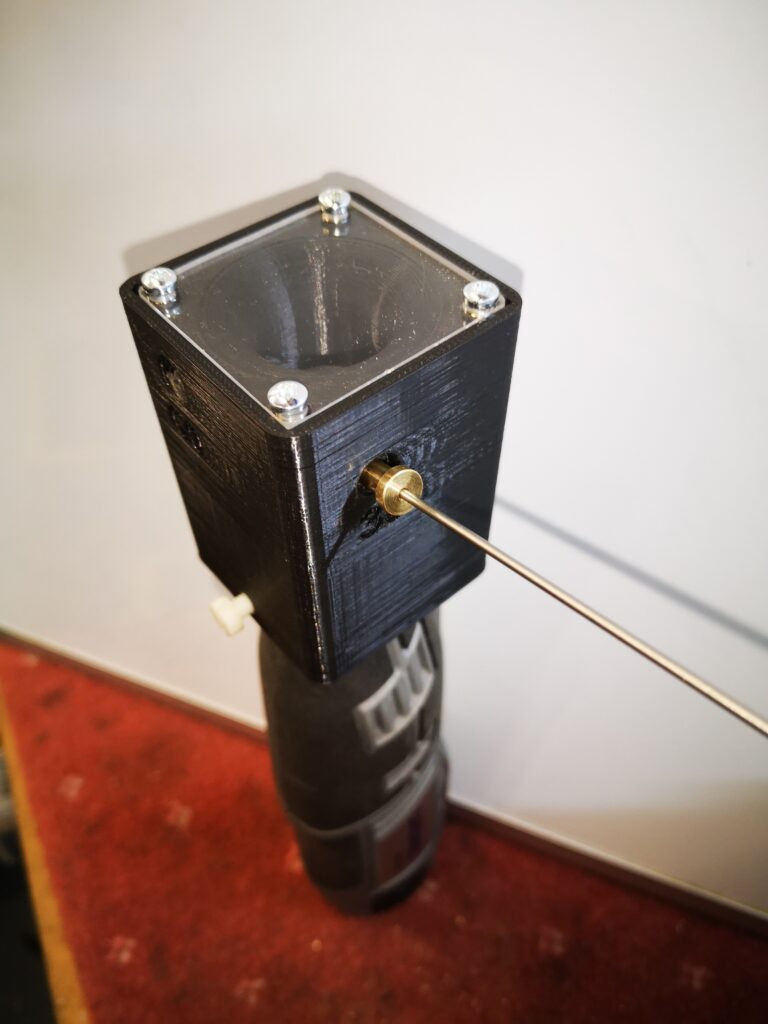
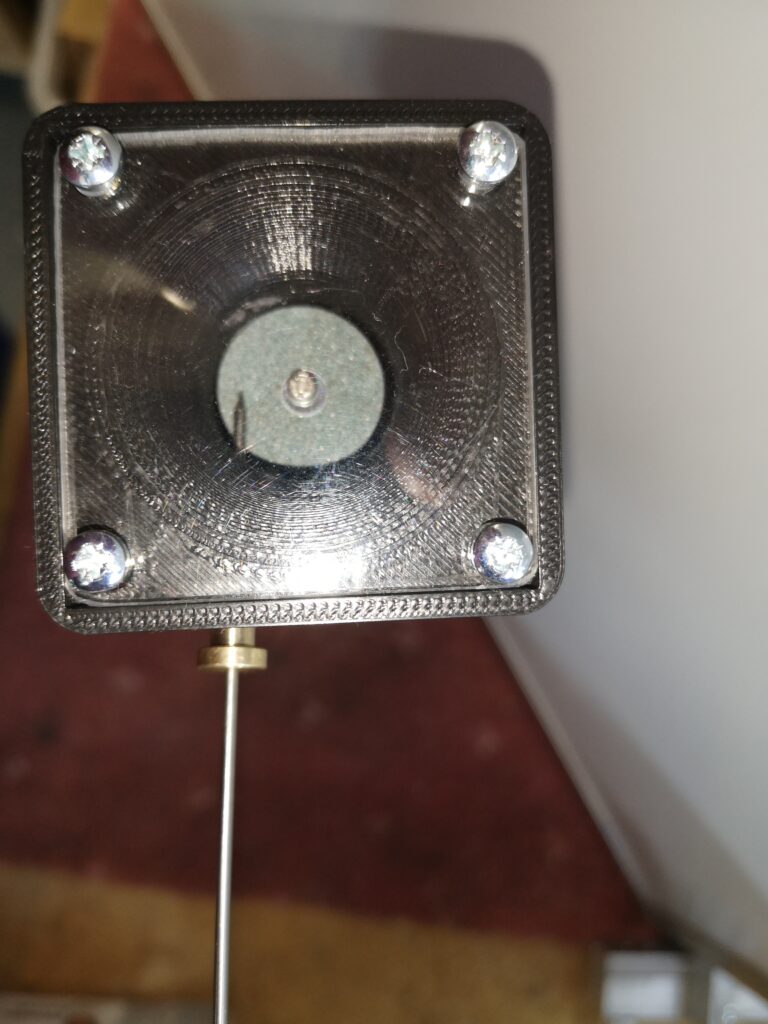
Read the full write up on this project as a PDF download
Tungsten Grinder using a Dremel
Similar or related subjects : –