Open Filament guide tube and adapters
I recently posted about the conversion of our Sindoh 3DWOX 3D printers to allow open source filament use. One benefit of the conversion is that it allows the filament reel to sit in an external reel box such as a ‘hot box’ dryer from where it is fed direct into the printer. This has resulted in filament being fed much more reliable than it had been using the printer internal cassette system.
On my setup I had a couple of clangs where the exposed filament between the ‘hot box’ and the printer got knocked and damaged. My solution to this has been to 3D print two filament interfaces to allow a PTFE protective feed tube to be used.
The first of these printed interfaces is a push fit into the Sindoh printed adapter. The Sindoh adapter performs two functions in the absence of the printer cassette. It provides a guide to feed the filament into the printer and also overrides the filament detector flap. The filament feed aperture in the Sindoh adapter is quite wide and I designed my printed part to push into their guide and provide a 2mm feed hole to more accurately ‘aim’ the filament. This feed hole enlarges to a 4mm section that is a push fit grip on 4mm PTFE tube. Note that dependent on print quality you might have to open out this hole and the 2mm hole to suit the OD of the PTFE tube and the filament. Be careful as the 4mm section does not go all the way through the print leaving a short inner 2mm section.
The 3D printed adapter on the ‘hot box’ mounts a M6 threaded pneumatic fitting that grips the end of the PTFE tube. This is fixed over the existing ‘hot box’ exit hole and aims the PTFE tube exit downwards. I drilled and tapped four M3 mounting holes in the plastic wall of the box base wall to mount the adapter. It sits straddling the base/lid interface line. This allows the box lid to still be opened. The images below show the Fusion screen shots and the final connected assembly.
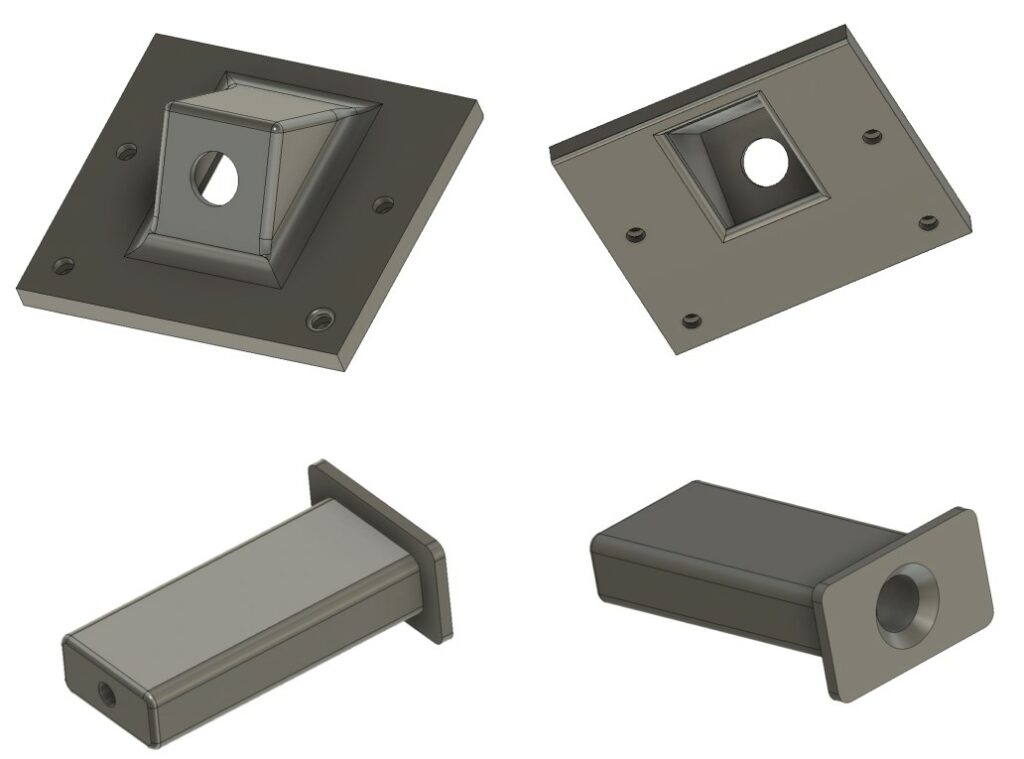
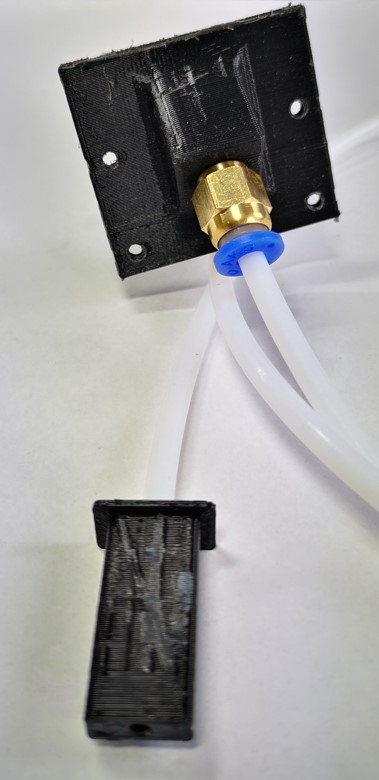
The solution works very well. The length of PTFE tube can be tweaked to suit the physical relationship between the printer and the ‘hot box’. The tube also gives added moisture protection to the filament when it could be exposed to humid air between printer runs.
These two small adapters have made the filament feed much more professional and the new arrangement has removed the danger of accidental filament damage.
The only problem with external feed to the Sindoh is that the door on the printer can no longer be closed so I need to work on a plan where to drill a suitable slot in the door….
The link below is a ZIP file with the associated files as both Fusion 360 and STLs plus the Sindoh open filament adapter files which were part of the Open Source documentation.
Links to similar or related post are listed below : –
- Qidi Slicer auto support error on my part
- Qidi X Smart 3 revised fan installation
- Qidi X Smart 3 tweaks
- Qidi X Smart 3 special weekend pricing
- Stop losing Qidi ifast 3D prints down the chamber front gap
- Fitting a Bento air filter to a Qidi ifast 3D printer
- 3D Printed Brass Threaded Insert Soldering Iron Stand
- eSUN filament reel silica drying pod
- Sindoh 3DWOX filament feed upgrade
- Sindoh DP200 conversion to Open Material