Frustration and headscratching but Qidi Support to the rescue
My two Qidi X Smart 3s have been a good investment but like all things, they are only as good as their ongoing performance.
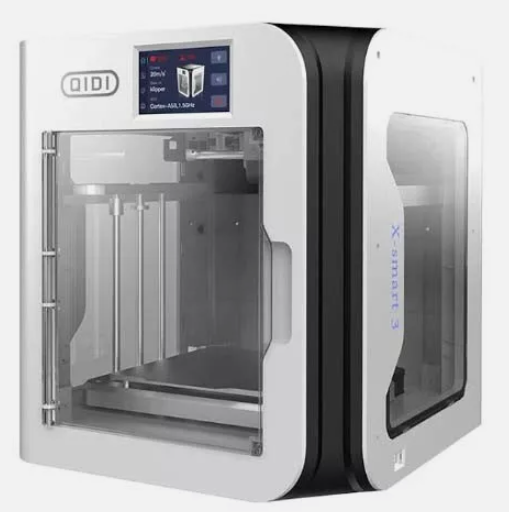
I recently had a few instances whereby my UK based printer stopped mid print having lost comms. This was the error message.
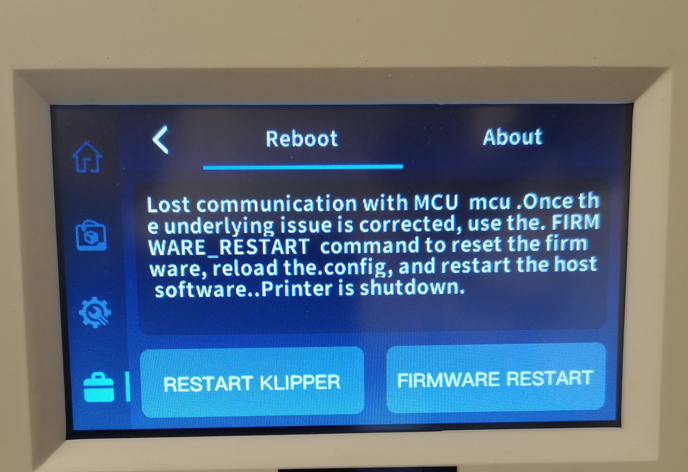
This error increased in frequency to the point where this message was present from switch on. In the process of this I learned that a good pointer to this problem is zero temperature readings on the opening LCD status screen.
Now at this point I must emphasise that in my experience Qidi support is excellent.
I opened a support dialogue with Qidi and between us we began to analyse the issue. The general initial consensus was that it was likely to be the USB-C umbilical cable connecting the motherboard to the print head. Other things that they suggested I test were whether I had too many files stored on the machine (weird one) or a hot end fan or the nozzle heater having gone short circuit both of the latter would lead to a high current demand via the USB-C. These were easy to test and checked out OK.
Focus therefore moved to the USB-C cable. This carries the power suppy to the hot end together with the control and measurement data stream between the motherboard and the hot end adapter board. The cable tested faulty (see the tester details below). To elimate whether this was the only fault I externally connected a uGreen equivalent USB-C cable but the MCU fault was still present.
The conclusion Qidi and I collectively arrived at was that there was an additional fault either with the motherboard or the adapter board.
Qidi sent me replacements items on a fast delivery from China at no cost to me. This is an example of the level of support you get from Qidi.
On receipt of the shipment it was a matter of substituting each item in turn to identify the culprit. This revealed that I had not just a faulty USB-C cable but also a faulty motherboard. The USB-C cable has to withstand a lot of flexing as the print head zooms around the chamber so I think this might have led to a fatigue related failure of the cable. I wonder also if the cable fault caused some form of knock on transient spike that damaged the motherboard.
While diving in and changing these components might seem a bit daunting, there is really no difficulty swapping them out. Remember to take a picture of everything before you commence. By far the most tricky aspect was physically removing and replacing the USB-C cable as it weaves its way round the build chamber via various slots in the cabinet.
One thing to note is that replacement motherboards, once fitted and working, may need to have their firmware updated to present issue. This is a matter of downloading the new file from the Qidi website. You have to unzip the file (a *.rar compressed file which is WinZip compatible) and then copy the file to a USB stick which you in turn plug into the printer USB port before following the onscreen instructions. Note it is important how you load the file on the memory stick in order for the auto update routine to initiate.
One outcome from all this activity is that I would recommend a USB cable tester. I bought one in from Amazon which is very analytic and immediately showed me I had a dead cable. For GBP16 this will certainly remove any future frustration caused by damaged cables.
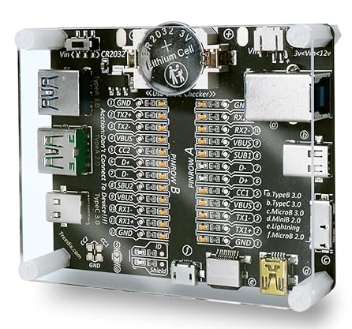
Overall not an ideal distraction from more important projects but as ever with this type of problem, you learn more about your workshop tooling and your associated knowledge base expands.
Thank you Qidi for all your help.
Links to similar or related post are listed below : –