I always used to make customised knobs in metal which had a knurled body with a piece of studding screwed and Loctited in place. It was good knurling practice and they looked fine until 3D printing came along.
I now have a variety of ‘styles’ for knob bodies modelled in Fusion 360. These have a hexagonal profile recess together with either a threaded hole or clearance hole modelled into them. A nut is Loctited onto the thread and then the thread with the nut in place SuperGlued into the 3D printed body.
As usual I’m all for an easy (a.k.a. lazy) way of doing things …. here is a Fusion image.
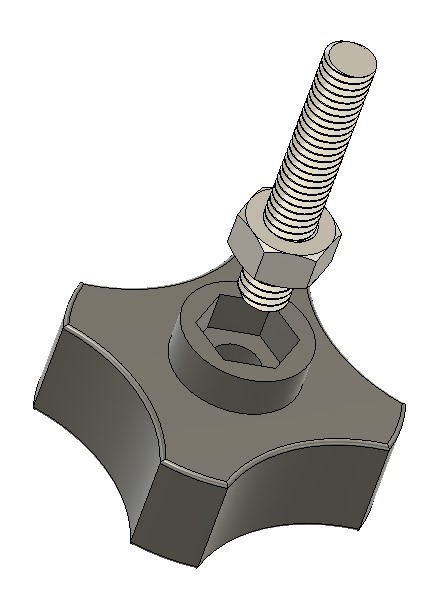
Similar or related subjects : –
- Qidi Slicer auto support error on my part
- Qidi X Smart 3 revised fan installation
- Qidi X Smart 3 tweaks
- Qidi X Smart 3 special weekend pricing
- Stop losing Qidi ifast 3D prints down the chamber front gap
- Fitting a Bento air filter to a Qidi ifast 3D printer
- 3D Printed Brass Threaded Insert Soldering Iron Stand
- eSUN filament reel silica drying pod
- Sindoh 3DWOX filament feed upgrade
- Sindoh DP200 conversion to Open Material