Understanding what was happening and why
I have a Bambi PT50 air compressor in my workshop. I chose it on the basis of being relatively quiet and having the capacity to provide sufficient air for my Fogbuster coolant system while working within the compressor’s specified duty cycle. The PT50 has dual compressor motor pumps.
The PT50 works very well. It is an oil free compressor and only needs the moisture bleed as a regular maintenance activity.
Of late I ran into an issue with air leaking from under the Condor MDR1 controller. This led to an investigation of how the compressor control process works, something I had not given much thought to while the unit was working fine.
The process, when working properly, is that the compressor motors push air into the air reservoir (tank) via a non return valve (NRV). When the pump stops the NRV seals the pump feed into the tank. The air contained can then only exit the tank via the MDR1 controller. When the air pressure in the tank drops due to demand and to a defined level (set by the controller) then the pump kicks in again and tops the tank up. A simple looping process.
The controller has a rubber diaphragm that expands and retracts subject to the pressure level in the tank. This diaphragm pushes on a hinged plate that acts as the trigger for the electrical switch that turns the pump motors on and off.
There is a secondary process to this.
When the pressure level in the tank reaches the point where the pumps need switching off, the NRV closes but there still remains a high pressure in the feed pipework from the pump to the NRV. This pressure will put stress on the pump motor when it next tries to start up. In the extreme this back pressure could cause a pump motor to stall.
To overcome this there is a tiny bleed valve in the controller that gets triggered to open simultaneously with the point where the pump switches off. The bleed is triggered by the same hinged plate mentioned above. The bleed valve is connected via a small tube that tees off the NRV in the feed from the pump motor. When triggered the valve vents the high pressure in the pump feed pipe to the NRV. This cause the sudden burst of air you hear when the pump switches off at its high pressure trip point.
So onto the problems that might occur.
The NRV seal can become damaged or worn or contaminated with debris from the reservoir tank. This means it will not seal when the pump switches off and the air in the tank will vent back out past the NRV, pass along the thin tube feeding the bleed valve and manifest as a continuous rush of air similar to the ‘switch off burst’ mentioned above. To summarise the fault – the pump switches off and you hear air continuously escaping. Solution – NRV valve damaged or contaminated and therefore not sealing. Check, clean and / or replace the valve.
The second problem is where there is air escaping from under the controller but only when the pump is running. (It is important to note that this does sometimes occur naturally when the pump is first switched on with an empty tank. In this situation there will perhaps not be enough pressure at switch ON to close the NRV. Once a few seconds of pumping has occurred the NRV should close). If the air continues to leak from bleed valve under the controller with the pumps running then this means the tiny needle that activates the bleed is either jammed with debris or the diaphragm / hinge plate in the controller is damaged. Note that on the MDR1 you can remove the valve to check it. The valve is enclosed within the black body of the bleed pipe mounting gland. It is twist locked in position.
In summary therefore : –
Air escaping from under the controller when the pump is not running suggests the NRV needs checking and / or replacing as needed.
Air escaping from under the controller when the pump is running suggests a problem with the needle bleed valve or the diaphragm / hinge plate in the controller. This is a more serious problem. It will cause the pump motors to overheat while trying to deliver air that is continuously escaping from the bleed valve. The MDR1 is not user repairable and is a crimped sealed unit. The picture below shows the MDR1 internals and the NRV.
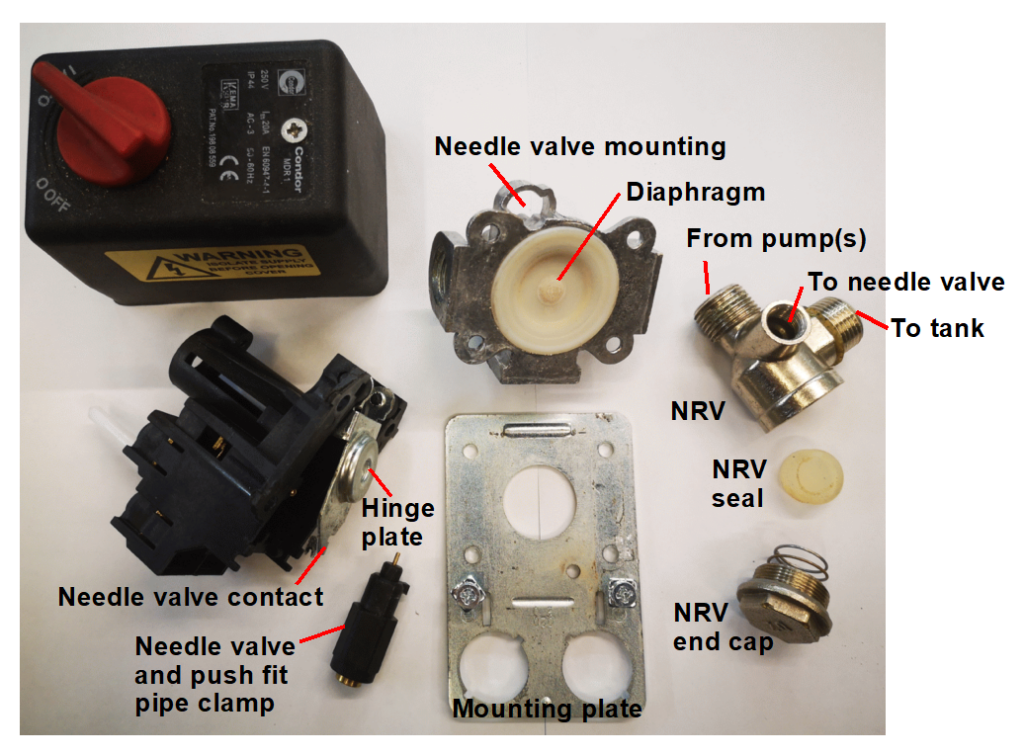
The first glance the cost of replacing the NRV or the MDR1 controller will appear similar but do take time to shop around. Replacing either of these will involve disconnecting various associated pipe fittings. As ever, take a picture before you start disassembling. Thoroughly clean all the parts before re-assembling. Use a sealant such as Loctite 577 to achieve quick and easy air tight seals.
Finally a word of warning – compressed air is a dangerous medium. Before undertaking any remedial work on a compressor you must ensure that the reservoir is fully vented and empty.
Links to similar or related post are listed below : –
- Eccentric Engineering Turnado freehand turning tool
- Rotring 300 2mm clutch pencil modification
- Kindling Cracker – a safer option
- SINO SDS2MS DRO repair
- A useful Amazon sourced small item storage system
- 3D Printed Threads Modelled in Fusion 360
- Three axis stepper controller PCB in stock
- Myford Super 7 Large Bore depth stop
- Tangential Lathe Toolholder for Myford Super 7
- Hemmingway Sensitive Knurling Tool