Threads not quite to the design plan
The other day I modelled an adapter boss that had a threaded end to fit a standard CCTV camera mounting box (GB Pipe Thread – 26.441mm x 1.84mm tpi) and with the other end to suit a 20mm flexible conduit. Here is a Fusion pictorial view.
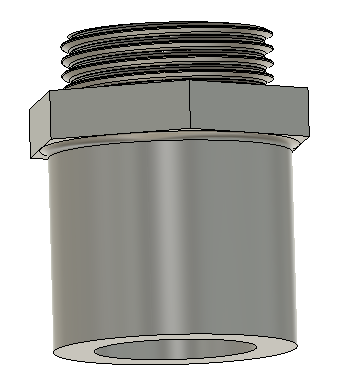
I modified the thread profile as per my post on thread tweaks and posted the file to Qidi Slicer. I opted to print in the orientation as shown above. This clearly needed support under the shoulder so without thinking I ticked the auto support tick box and hit print. The thread was a disaster flecks of filament such that it did not mate with the camera mounting box threaded hole.
Head scratching time, what had gone wrong ?
I had thoughtlessly just ticked autogenerate support and Qidi Slicer saw the thread profiles as potentially needing support and hence all the flash filament. Re-running with ‘support on build plate only’ removed the problem. See below.
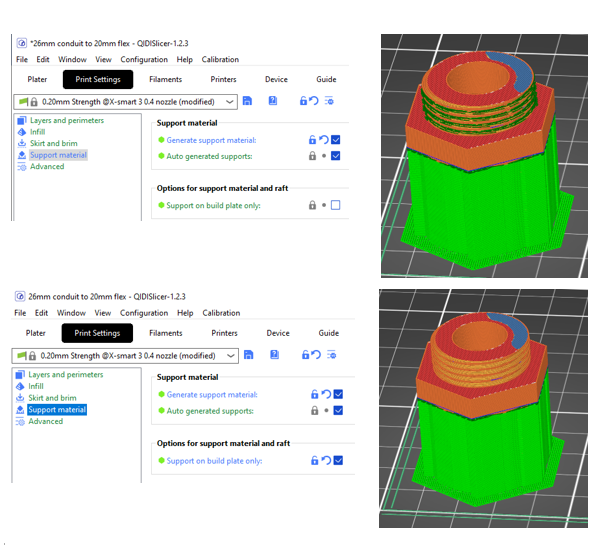
This problem probably become more apparent due to the large size of the thread being modelled. Probably a dumb thing to have done but I tend to learn more from doing dumb things. One issue to be aware of in the future.
Links to similar or related post are listed below : –
- Qidi X Smart 3 revised fan installation
- Qidi X Smart 3 tweaks
- Qidi X Smart 3 special weekend pricing
- Stop losing Qidi ifast 3D prints down the chamber front gap
- Fitting a Bento air filter to a Qidi ifast 3D printer
- 3D Printed Brass Threaded Insert Soldering Iron Stand
- eSUN filament reel silica drying pod
- Sindoh 3DWOX filament feed upgrade
- Sindoh DP200 conversion to Open Material
- Joining PLA filament
Alan, Thanks for your link to this. It is something for me to keep an eye on.
I have been busy prototyping a spindle lock for my KX3 using carbon fibre enhanced filament. So far it seems to be holding up.
If interested, I’ll upload to the ME site.
Rgds, Matt
Sounds good Matt, I’ve never tried CF filaments so will be interested in seeing your results.
Will let you know any further revelations …
Regards
Alan