A Hybrid Version of John Moran’s Elegant Design
While investigating four facet drill sharpening, I came across John Moran’s website which detailed his design for a four facet drill sharpener. Four facet sharpening is popular for providing more accurate starting of a hole, less drilling pressure, more accurate hole size and better retention of drill point sharpness. John’s design is intended for sharpening 2mm to 12mm drill bits.
I have a Quorn grinder but it is not something that I can quickly pull out from under the bench to sharpen the odd drill. John’s design looked easy to set up and use and certainly easier to carry. I have been working with him to produce this hybrid version. I recommend that you read John’s write up before embarking on either his original design or my 3D printed hybrid version. He also presents a YouTube video on how to use the sharpener.
https://gadgetbuilder.com/DrillSharp.html#Facet4
Here is a picture of John’s finished design. Very nicely finished and presented.
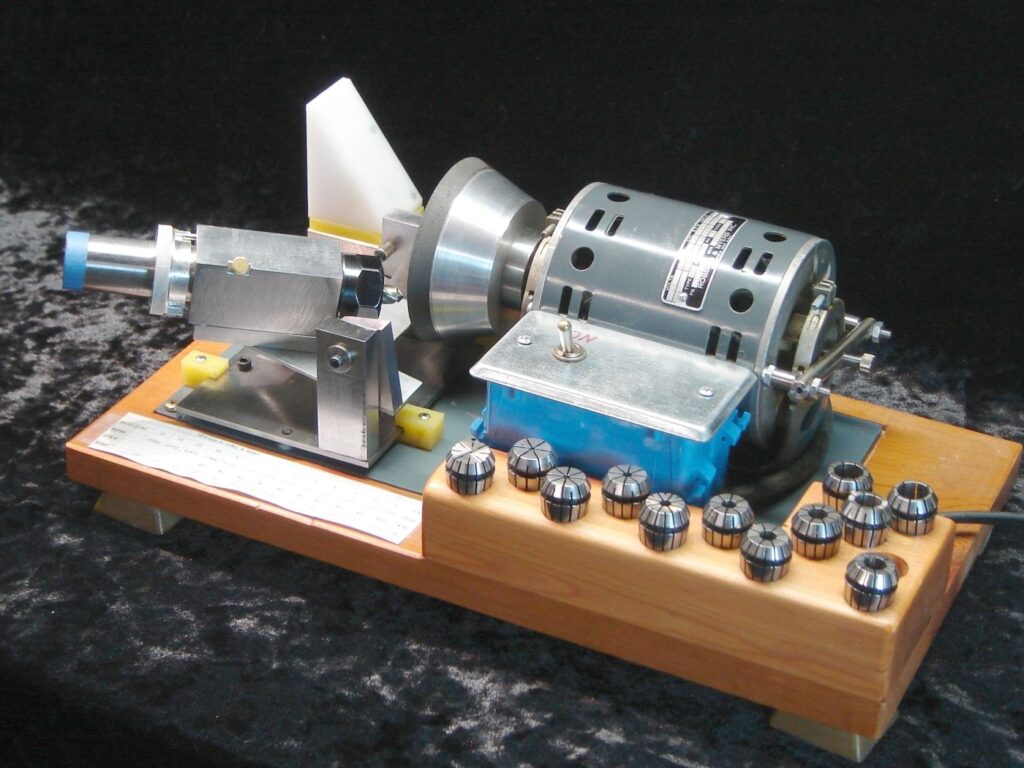
Here is a picture (not quite so pretty …) of my 3D printed hybrid version. A new baseplate might be in order to smarten it up.
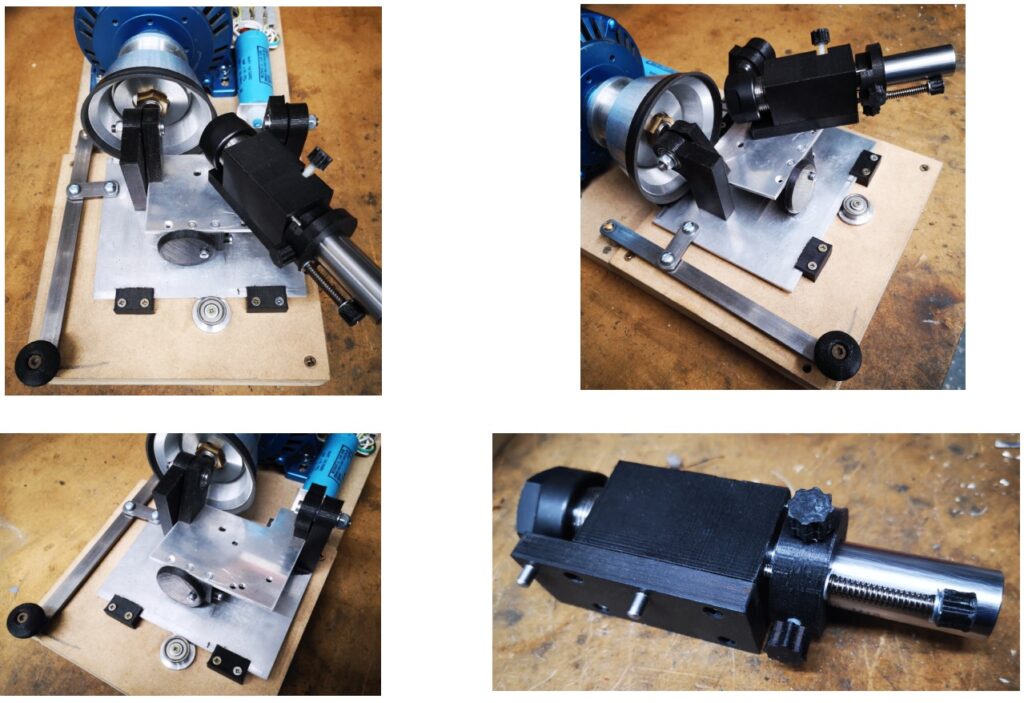
The concept of combining 3D printed components with essential metal parts works very well and the resulting sharpener appears to be stable and repeatable in its results. There is a huge advantage in combining technologies in this manner. All the ‘boring’ or ‘dreading to make / leave until tomorrow’ parts are easily produced on a 3D printer and the remaining metal parts are straightforward to produce with conventional resources and skills.
Rather than go into details as a blog post, below is a link to a ZIP file that contains my full write up, 2D PDF drawings of the metal parts, STEP files of the 3D printed files and the raw Fusion files for those wanting to tweak.
If you can’t work with STEP files then let me know and I will run STL versions. STEP files are more accurate than STLs and also have the advantage of being more easily editable than STLs.
I think you will be impressed with the end result of John’s design.
If this write up or my general waffle is of interest then please subscribe to receive notices of new posts. If you build the sharpener and it works let me know. If it doesn’t work and it’s my fault for not providing enough information than email me so I can correct things.
As an alternative to a 3D printed version you can watch Mark Presling on YouTube who has recently construct the same sharpener in metal.
UPDATE
I have already had some feedback on the 3D printed design so some of you are quick off the mark.
This feedback related to the friction of the collet holder shank in the block and also the print roughness against the depth setting screw. Both of these will relate to the print quality from your printer.
As an experiment I ran a new version of the block with a larger bore and then lined it with an aluminium sleeve that was a smooth fit on the shank. I also turned a flange on the end of this sleeve so that the adjuster nut had a smooth metal surface to ride against.
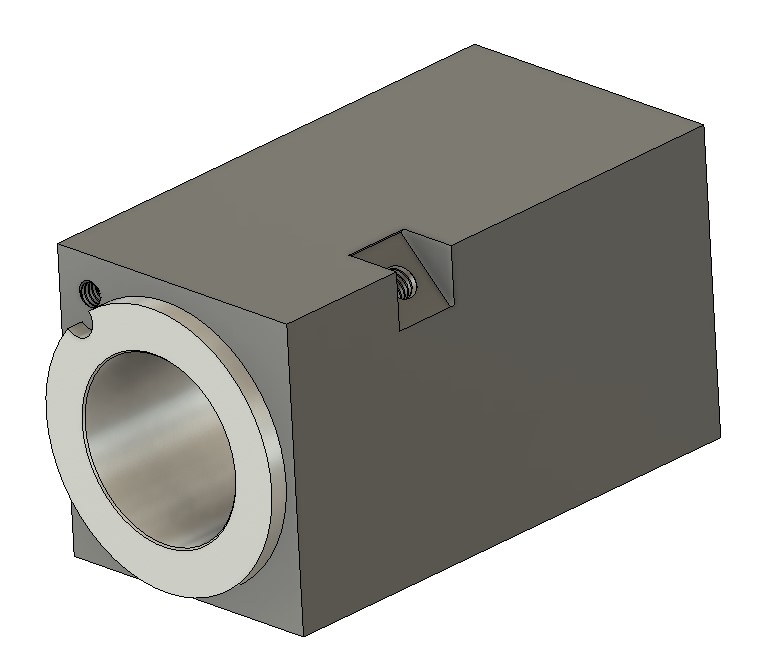
The addition of the sleeve looks promising in solving these two issues. I admit it is going against the concept of a 3D printed set of parts but the sleeve is easy to turn up on the lathe and the new block in PLA is still much easier to produce that trying to make the block totally in metal.
You can download the edited write up, new collet chuch holder block STEP and the sleeve drawing in this add on ZIP file.
Links to similar or related post are listed below : –
- Qidi Slicer auto support error on my part
- Qidi X Smart 3 revised fan installation
- Qidi X Smart 3 tweaks
- Qidi X Smart 3 special weekend pricing
- Stop losing Qidi ifast 3D prints down the chamber front gap
- Fitting a Bento air filter to a Qidi ifast 3D printer
- 3D Printed Brass Threaded Insert Soldering Iron Stand
- eSUN filament reel silica drying pod
- Sindoh 3DWOX filament feed upgrade
- Sindoh DP200 conversion to Open Material
- Qidi Slicer auto support error on my part
- Qidi X Smart 3 revised fan installation
- Qidi X Smart 3 tweaks
- Qidi X Smart 3 special weekend pricing
- Stop losing Qidi ifast 3D prints down the chamber front gap
- Fitting a Bento air filter to a Qidi ifast 3D printer
- 3D Printed Brass Threaded Insert Soldering Iron Stand
- eSUN filament reel silica drying pod
- Sindoh 3DWOX filament feed upgrade
- Sindoh DP200 conversion to Open Material