A good reason why not to leave a parallel on the way cover
I was running a milling job on my 440 the other day and I had left a parallel on the Y axis front way cover when I had switched off in the evening. Next morning I switched on and homed the axis in the usual order of X axis and then the Y only to hear a crunch as it reached the homing position. The parallel had got jammed under the table front shroud. I reversed the motion, removed the parallel, homed Z and carried on.
Fast forward to the next day. Switched on and homed X which resulted in a very bad end stop stepper chatter. I stopped the motion and moved the X axis back. Something bad had happened. I stripped off my machine vice and my tooling table and removed the table front cover. The limit switch had been crushed, presumably by the parallel the previous day.
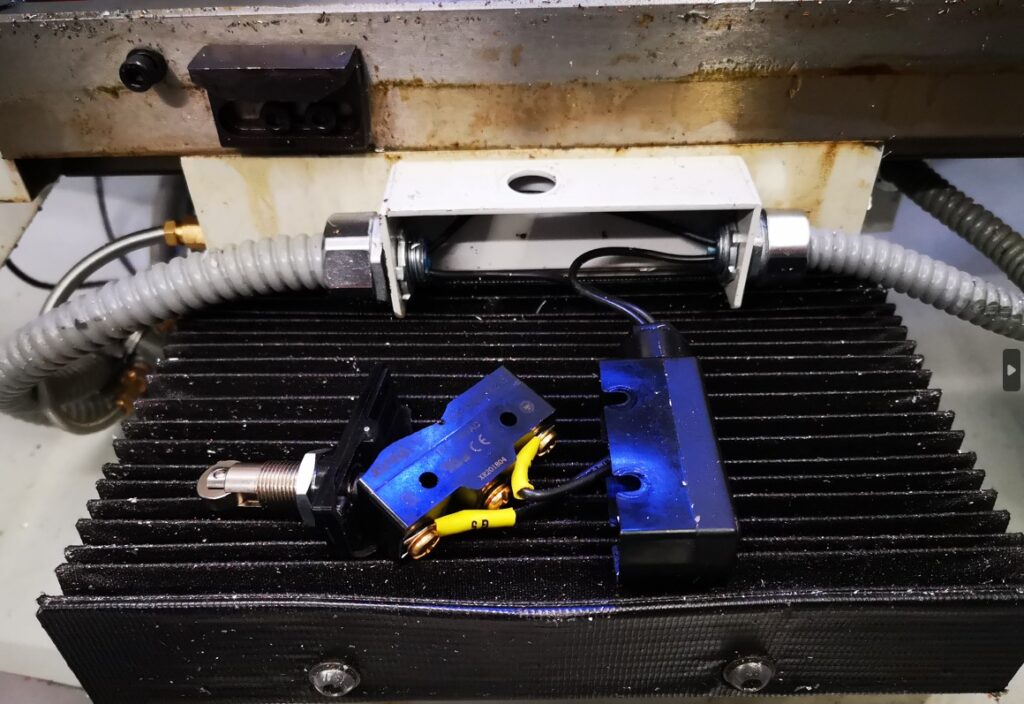
I’d like to say that this is the first time this has happened …. but it isn’t. (Hence the ding in the cover front edge …). A quick check on Amazon revealed quite a few identical looking replacement switches. There was also a twin pack available from China for much the same price but clearly much longer delivery time. A new switch was ordered and all is now up and running again (after re-tramming the tooling plate and then the mill vice etc etc …. what a pain ….)
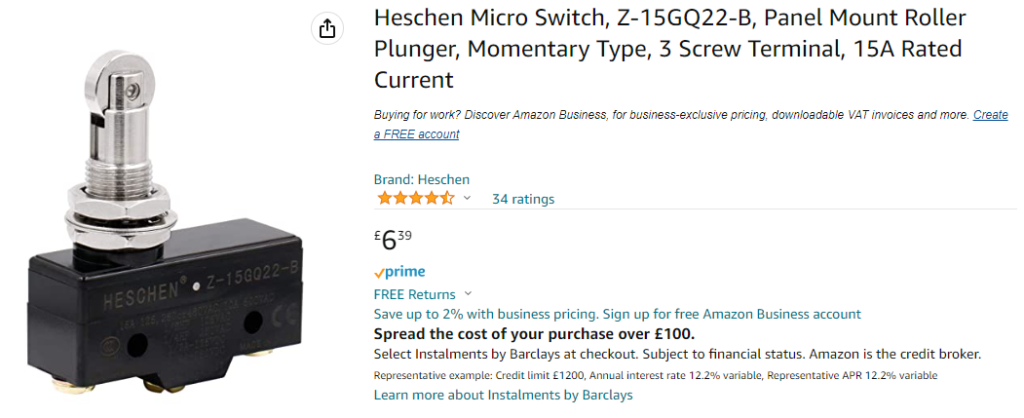
In passing I do keep pondering the 440 limit switches and wondering if I could replace them with inductive sensors but it all looks a bit difficult having to sort out the additional wiring needed. Maybe another day ? (Sadly such a modification would still not stop me stupidly leaving things on the way cover ….)
Links to similar or related post are listed below : –
- MX3660 as used on Tormach PCNC440
- Tormach Power Drawbar piston service
- Notepad ++ for GCode Editing
- Local power USB switching circuit
- Tormach PCNC440 X Axis limit switch repair
- Experiences CNC machining Aluminium Composite Material (ACM)
- Enclosure finally added to my Tormach PCNC440
- CNC Work Reference Centring using Mushrooms
- Clough42 Electronic Leadscrew Project Implementation Notes
- Floating pressure foot for the CNCEST3040T mini milling machine
- MX3660 as used on Tormach PCNC440
- Tormach Power Drawbar piston service
- Notepad ++ for GCode Editing
- Local power USB switching circuit
- Tormach PCNC440 X Axis limit switch repair
- Experiences CNC machining Aluminium Composite Material (ACM)
- Enclosure finally added to my Tormach PCNC440
- CNC Work Reference Centring using Mushrooms
- Clough42 Electronic Leadscrew Project Implementation Notes
- Floating pressure foot for the CNCEST3040T mini milling machine