I have been avidly watching Clough42 on YouTube. James comes over as a really nice guy and his presentation of his projects is excellent.
My principle interest is the Electronic Leadscrew modification to lathes. When installed this removes all the hassle of gearboxes and look up tables to be able to cut both Imperial and Metric screw threads and to set X axis movement feed rates.
The concept is simple but his implementation is second to none. A rotary encoder is fitted to the spindle to count revolutions of the chuck and a stepper motor (or servo hybrid) controls the rotation of the leadscrew. The resulting feed speed is derived from look up tables. The whole installation is controlled by a Texas Instruments LaunchPad C2000 microcontroller development board.
I have documented how I implemented this on my Myford Super 7 Big Bore lathe and the pdf can be downloaded below. There is also a ZIP file of all the Fusion related models for either CNC or 3D printing.
Electronic Leadscrew on Myford Super 7
Minor edits added to v3 relating to programming the servo controller
Electronic Leadscrew on Myford Super 7 v3
Electronic Leadscrew Fusion 360 Files
Updates : –
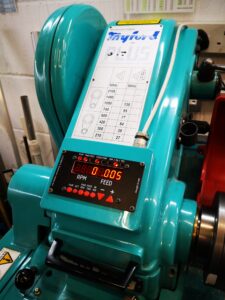
Since installing the ELS I have incorporated thrust bearings on the leadscrew mounting. This impacts on the coupling to the stepper motor.
Similar or related subjects : –
- Notepad ++ for GCode Editing
- Local power USB switching circuit
- Tormach PCNC440 X Axis limit switch repair
- Experiences CNC machining Aluminium Composite Material (ACM)
- Enclosure finally added to my Tormach PCNC440
- CNC Work Reference Centring using Mushrooms
- Floating pressure foot for the CNCEST3040T mini milling machine
- Probes and Haimer Taster Modification
- Arc and Circle I and J code calculator for GCode cutting paths
- Tormach PathPilot G37 Update
Nice write up, thanks for taking the time.
Thanks Phil. Had a look at your site and see you’ve done some nice things.
Woody