A PLA version of Preso’s versatile clamping system
Sometimes I think I am way out of touch when I suddenly find a new interesting YouTube maker site that had gone completely under my radar. Mark Presling is based in Australia and has some interesting projects and ideas on his YouTube vlog. My thanks go to Peter in Croatia for pointing me in Mark’s direction.
Mark’s latest post (Jan ’23) focussed on a work hold down clamping system using a variant of a ClickSpring eccentric screw and block concept. This looked quite interesting and was timely with my experiments with the Gack clamping idea.
I’m still in France, slightly idle but with Fusion 360 as ever close to hand. Mark’s post does not precisely detail the dimensions but I got a rough feel for proportions and modelled my interpretation of his clamp idea in Fusion. To give the eccentric screw clamp holding strength I embedded a M8 nut. The brass clamping block would remain the same as in Mark’s design and for clarity is not shown on the images below.
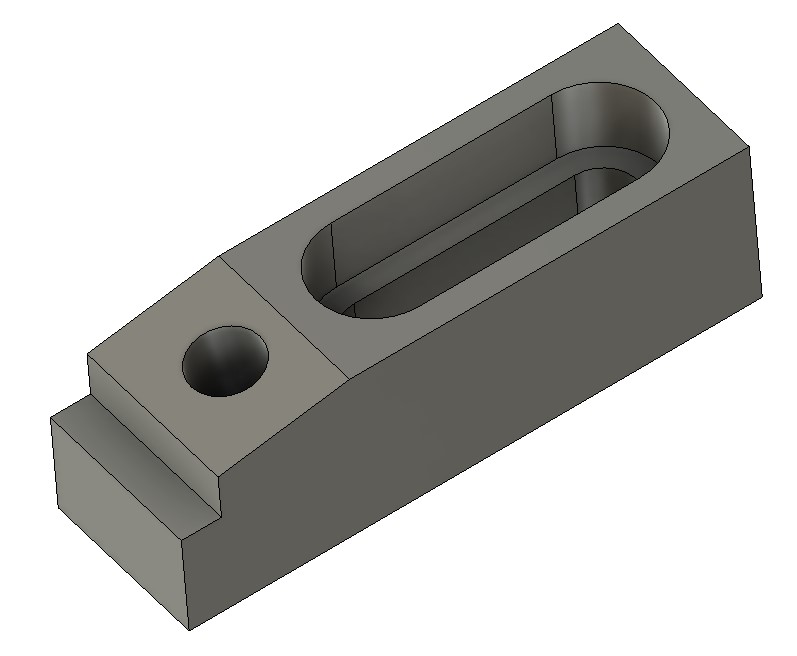

I sent some graphics and a STEP file off to Mark for his thoughts and we both agreed that a PLA or PETG version would work and probably be a simple low cost source for hold downs on many CNC router tables. Mark mentioned this in Part 2 of his video post.
Variants could be quickly made for different geometries to suit the work in progress. Like my Gack 3D print, the clamps would not stand up to serious full on metal CNC grunt milling but router table based profiling would be fine. The advantage a 3D printed clamp is that cutter dings when hitting the plastic would not do any damage to the tool. (I realise that none of us ever do that anyway ….).
In the ZIP file below there is a STEP and STL file of my interpretation of the clamp and also the Fusion 360 file for those wanting to play further.
I won’t be able to print the idea myself until I get home. I think it will need a vertical print to avoid the need for support material.
Links to similar or related post are listed below : –
- Qidi Slicer auto support error on my part
- Qidi X Smart 3 revised fan installation
- Qidi X Smart 3 tweaks
- Qidi X Smart 3 special weekend pricing
- Stop losing Qidi ifast 3D prints down the chamber front gap
- Fitting a Bento air filter to a Qidi ifast 3D printer
- 3D Printed Brass Threaded Insert Soldering Iron Stand
- eSUN filament reel silica drying pod
- Sindoh 3DWOX filament feed upgrade
- Sindoh DP200 conversion to Open Material
- Qidi Slicer auto support error on my part
- Qidi X Smart 3 revised fan installation
- Qidi X Smart 3 tweaks
- Qidi X Smart 3 special weekend pricing
- Stop losing Qidi ifast 3D prints down the chamber front gap
- Fitting a Bento air filter to a Qidi ifast 3D printer
- 3D Printed Brass Threaded Insert Soldering Iron Stand
- eSUN filament reel silica drying pod
- Sindoh 3DWOX filament feed upgrade
- Sindoh DP200 conversion to Open Material