The Tormach PCNC440 is a lovely machine and is more than big enough for my present needs. The one problem I had encountered was when coming to a tool change on a CNC job sometimes there was not enough Z height to get the TTS collet out of the spindle. This was particularly difficult when using larger diameter drill bits in a chuck style holder.
Once in program there did not seem to be any option to break the run and do a G30 or similar. What I really needed was a move of the spindle upwards and outwards to get it clear of the job and allow TTS access.
Reading up in Peter Smid’s excellent CNC Programming Handbook I could see that care was going to be needed to ensure that any movement was first of all a Z action and then X and Y to avoid the danger of crashing the tool into the job or its fixtures.
I had some discussion with John Saunders at NYC CNC and John was working on a video around this subject. He helped enormously.
The end result is to use G53 machine coordinates to first do a Z and then and X and Y to move the tool up and to the side for tool change access.
This involves edits to the post processor in three places. The first two edits (Lines 44 and 66) are there to give an option for this movement in the drop down selection box. (The line 24 edit is an earlier modification to allow Mill Turning – see separate post).
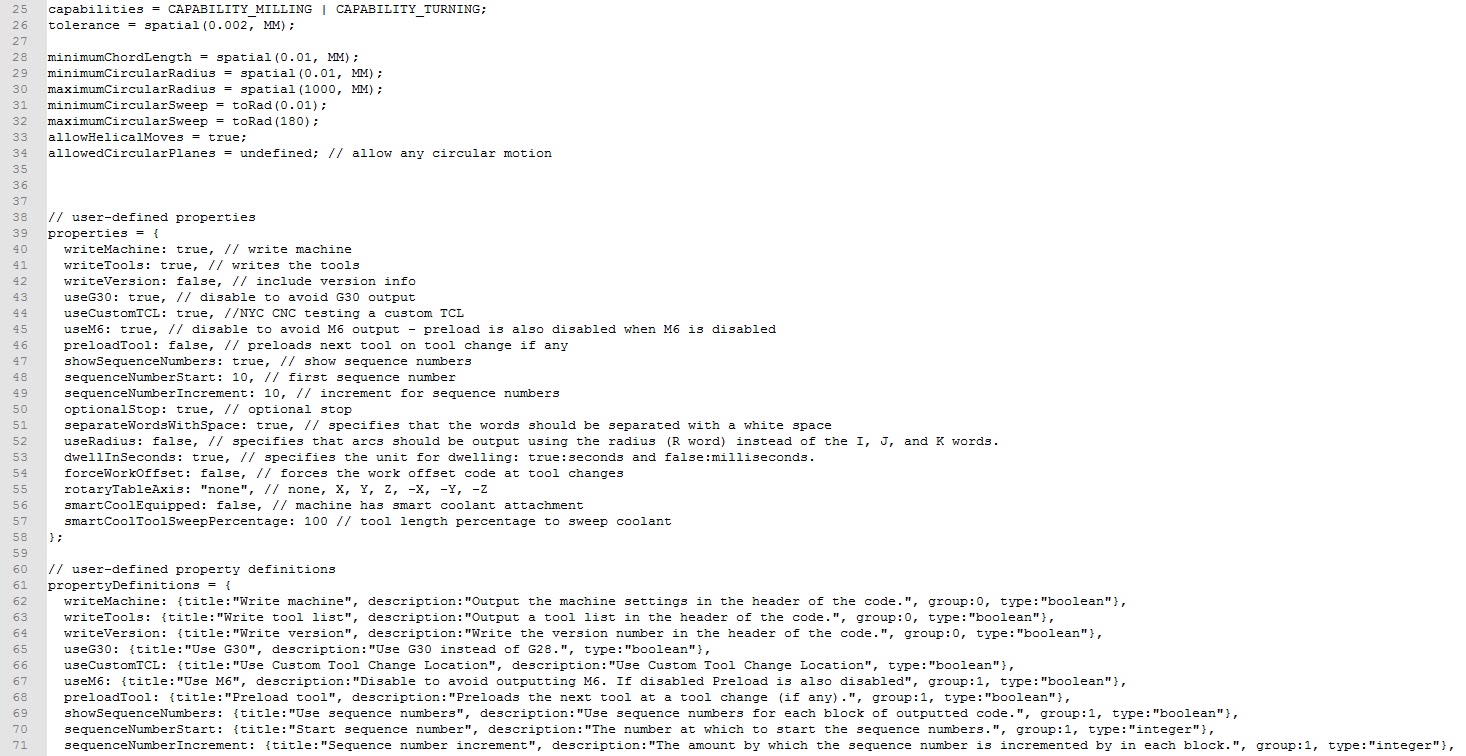
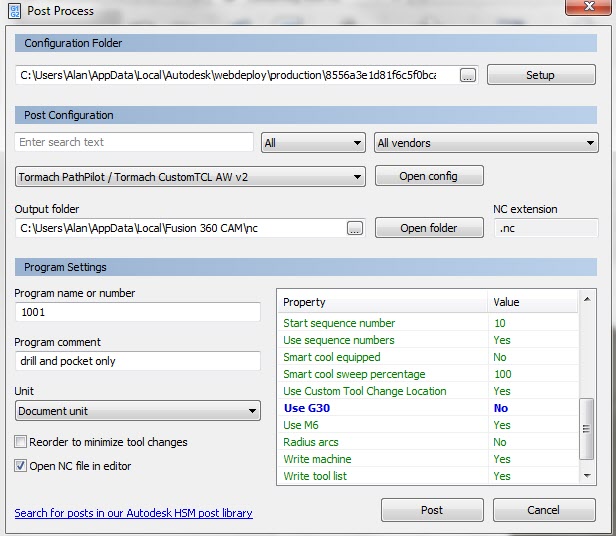
The third edit gives the instructions for this as a G53 Z move than a X and Y move (Lines 543-538). Note that I later found that I had to add a G54 after the G53 movements as some CAM actions did not include a G54 as part of a tool change.
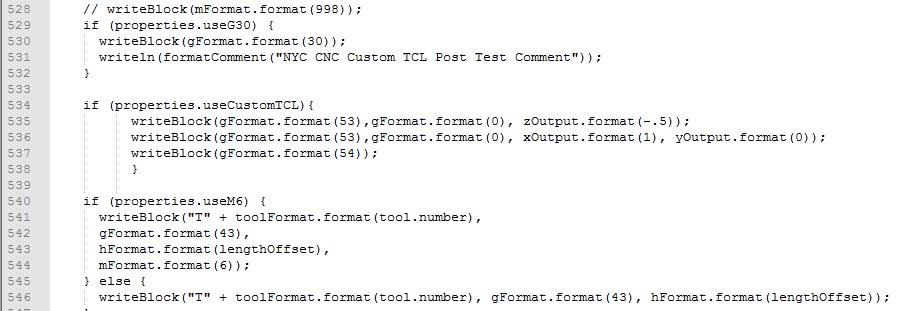
I later on decided it would be nice to include this G53 movement at program end so this is a fourth edit (Lines 1404 – 1405) and not forgetting the change for Mill Turning edit (Line 25) there are five changes in total.

That concludes the changes. I recommend that you spend time watching John’s videos on Post Processor edits on NYC CNC.
If you can’t read the edits then drop me an email and I can send you a full listing.
Note that these are changes to the Tormach standard post processor code and if you are tempted to do this you should do a ‘Save As’ on the original code and only edit the newly created and saved file so you have a fall back position. Likewise I accept no responsibility in documenting this and putting you up to potential mischief messing with your machine and causing damage.
Similar or related subjects : –
- Fusion Electronics Library Notes and Crib Sheet
- I had a ChatGPT experience
- Fusion Sheet Metal model export as PDF
- Drawing a parabola in Fusion
- Creating Customised Threads in Fusion 360
- Automated 3D printed collet storage using Fusion 360 parameters
- Fusion 360 Keyboard Shortcuts
- Creating a worm drive in Fusion 360
- Fusion 360 Parameter Lookup Sheet
- Adding Colour Coding to Fusion 360 Assemblies