Experiences so far with the Qidi
I’ve had the Qidi i-fast 3D printer for few days now and the printing results have been excellent with all manner of geometry. It is particularly good on thin wall models. I am getting more adept at filament management (loading and unloading) which is different to the Sindoh as there is not a cassette system on the Qidi.
The Qidi slicer is a skinned version of Cura and has a significantly larger number of settings to tweak than the Sindoh. That having been said the Qidi has a number of preset configs for different print types and qualities. So far I have not needed to change any of the small print settings on these.
There are some differences to my old Sindoh. When I post a file to the Qidi from Fusion, a memory stick needs to be in the Qidi for the file to post to. On the Sindoh the file would post to the machine memory and be stored internally. This change is not a problem and does mean that there is a listing of previous prints on the memory stick for repeat prints.
The printing plate on the bed is magnetically held in place and works well. Providing the bed plate is removed and allowed to cool down, the prints just ‘pop off’.
The Perspex top cover is held in place by magnets. It has no tactile means of gripping it when you try to lift it off. I have printed two handles and fitted these to the lid to overcome this. See below.
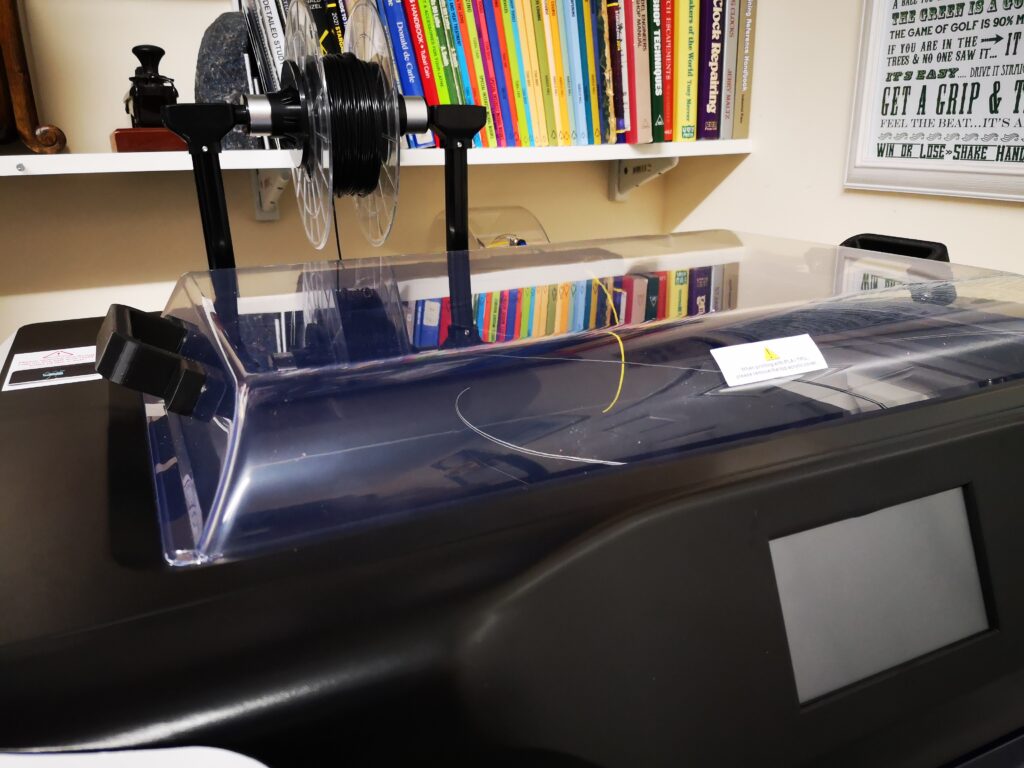
Filament reels can be mounted in a number of ways. There is a suspension bar at the rear of the printer that the reels can be hung on (see above image) or there are two brackets supplied to support two supplied filament boxes to be mounted on the rear of the printer. There is also a extra buy option of a Dryer Box that can also be hung from the suspension bar. The Dryer Box is quite useful for protecting pre-dried filament from absorbing moisture. Beware that the inner hole on the filament reel needs to be 52mm or more to fit inside the Dryer Box.
None of these mounting options worked for my restricted depth of bench space. Instead I use either the Dryer Box or one of the standard filament boxes sat on the bench alongside the printer. For this location I bought in some 4mm OD/2mm ID PTFE tubing as a longer guide tube for the filament. This works well.
The only minor frustration is the abundance of long thin PLA strings that result from the printer warm up preamble. They seem to get everywhere. The Sindoh used to manage this better with a small waste box and nozzle wiper.
Overall a lovely machine which should meet my needs for a long time to come.
Links to similar or related post are listed below : –
- Qidi Slicer auto support error on my part
- Qidi X Smart 3 revised fan installation
- Qidi X Smart 3 tweaks
- Qidi X Smart 3 special weekend pricing
- Stop losing Qidi ifast 3D prints down the chamber front gap
- Fitting a Bento air filter to a Qidi ifast 3D printer
- 3D Printed Brass Threaded Insert Soldering Iron Stand
- eSUN filament reel silica drying pod
- Sindoh 3DWOX filament feed upgrade
- Sindoh DP200 conversion to Open Material
- Qidi Slicer auto support error on my part
- Qidi X Smart 3 revised fan installation
- Qidi X Smart 3 tweaks
- Qidi X Smart 3 special weekend pricing
- Stop losing Qidi ifast 3D prints down the chamber front gap
- Fitting a Bento air filter to a Qidi ifast 3D printer
- 3D Printed Brass Threaded Insert Soldering Iron Stand
- eSUN filament reel silica drying pod
- Sindoh 3DWOX filament feed upgrade
- Sindoh DP200 conversion to Open Material