Like all responsible citizens we have been in social distancing since March and throughout this time both my wife and I have been concerned about our house in France.
As infection rates seemed to be easing we decided to make a quick visit to the Dordogne to check all was well. Normally we take a ferry crossing but we really did not want to risk the exposure this would entail. Instead we opted to take the Channel Tunnel. For those not familiar with this route, you drive to the terminal, check in and then get loaded in your car onto a rail transport shuttle train. The journey through the Tunnel takes around 40 minutes and you off load near Calais in France and head south. This route offered minimal exposure to others as we were effectively in the car from door to door and not allowed to leave the vehicle on the shuttle train.
We live in the mid south of England so there was the discomfort of a 2 hour journey to the Folkestone to board the shuttle. Normally we have a 1 hour run to Portsmouth for the ferry. Once in France at Calais there was a 9+ hour run via Paris (not fun) down to the Dordogne. It was tiring but with the two of us taking shifts it eased the strain.
All was good at the house and we spent two weeks with minimal human contact and survived on the French ‘click and collect’ food supply services. We had some very high daily temperatures and some nice wine.
We have a very close friend called John living in France and he knows our house well and envies our Dark Sky location. He has similar interests in Fusion 360, horology, Arduino, mechanical design and relevant to this instance, astro-photography. August is the peak time for the Perseid meteor shower. We both own Canon Powershot SX50 HS zoom cameras and he made a comment that it was a shame that these did not have a Bulb setting for the shutter or the ability for us to do time lapse to take some shots of the meteor trails.
Investigating on the internet revealed that there is a group of enthusiasts that have hacked the operating system of the Canon range of cameras. This is known as CHDK (Canon Hack Development Kit). It allows you to load a firmware update into the camera to expand its capabilities but does not overwrite the default issued code. The CHDK code is wiped once you switch off and the camera reverts to normal.
CHDK provides facilities for long exposure times and for time lapse routines. This therefore addressed both the issues we had with the SX50. It took a while for us to share notes and to get our heads around how CHDK worked and how to set it up. I managed to get my camera hacked the day before it was time to journey home. I had one last night of hopefully cloud free viewing to get some images.
Those familiar with all things astro will know that a long exposure time image of the sky will be degraded by the movement of the Earth’s rotation. The result is ‘trails’ on the stars so they look elongated rather than single dots. John is developing an Arduino based star tracker but I did not have access to this but I did have my Celestron telescope. When the telescope is calibrated and locked it will keep track of the star movement and not leave trails.
I spent the day devising a mount for the Canon on the telescope and come 10 pm all was ready to run … except the cloud cover was really bad. I waited and waited and finally I got one run of 4 shots of 3 minutes each looking at the Milky Way. Given more time these could have been stacked in Registax or similar to enhance the images further.
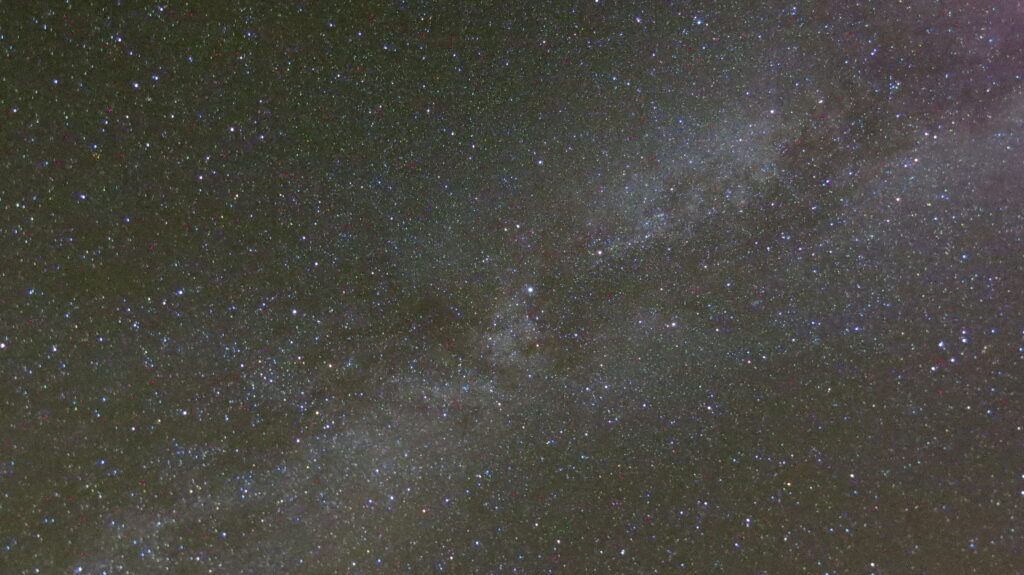
I accept that the SX50 is far from ideal as an astro imaging camera. There is too much glass in the light path and the filtering and noise will be poor but this was a first step along the road. I was pretty pleased with the result. I now need to compare notes with John on his Arduino based star tracker. Another project to add to the ever increasing list …..
Next day we made the house secure and departed knowing that we now faced not just a 13 hour journey but also a 14 day quarantine period when we got home. But of course the upside is 14 days of uninterrupted workshop time.
Similar or related subjects : –