This is nothing magic but worth a mention. Being fundamentally lazy I don’t like to assemble and solder electronic multi-way connectors. There is never enough room to work on the contacts and the cables never lay up how you would like them to. This could have course be a function of my eyesight ..
I am currently working on boxing and installing the Tormach USB Expansion Board which has a USB connector interface. I wanted the cable to pass through some form of gland into the box but didn’t want to cut a standard USB cable and remake the connector at one end of the other.
After some head scratching I came up with the following simple cable gland/cable grip. It is nothing revolutionary but made life easy and the parts only took 20 minutes to design in Fusion 360 and then 3D print on the Sindoh 3DWOX.
It has two identical semicircular halves that hold the cable and there is a ring that pushes over these on the outside of the box. A small flange holds these in place on the inside of the box. The hole in the box and the ring inside diameter are both 16mm to allow the USB connector largest dimension to pass through. This is also one of the standard cut rings on a cone cut hole drill which makes cutting the hole in the box very straightforward.
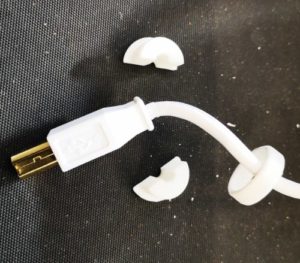
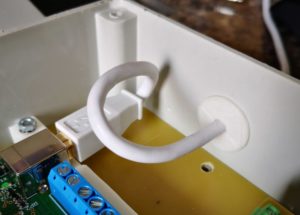
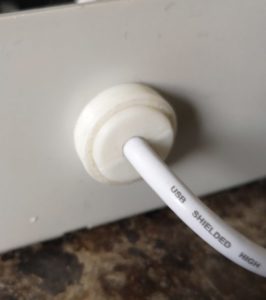
Not rocket science but you never know it might come in useful and the dimensions can be tweaked to suit other cables and connectors. Similar or related subjects : –
- Parting Off on the Lathe
- Workshop storage update using Spacemaster 5L boxes
- Plastic heat sealer – a useful workshop asset
- How to square up a scrap piece of stock ready for machining
- Deburring techniques in the home workshop
- First screw threads cut using Clough42 electronic leadscrew
- Machining a job that is outside a milling machine’s table travel using Fusion 360
- Stevenson Collet Block and the Angle of Dangle
- A Lazy Cable Clamp using 3D Printing
- Mill Turning Jig